In a conversation with Vikrant Rawa, Chief Technology Evangelist at Intriguity, a company offering high-tech solutions to the jewellery industry, Solitaire delves into the dynamic landscape of technological breakthroughs reshaping the Indian jewellery manufacturing industry. Rawa offers insights into the strides made over the last five years and anticipates the trends that will define the sector in the near future.
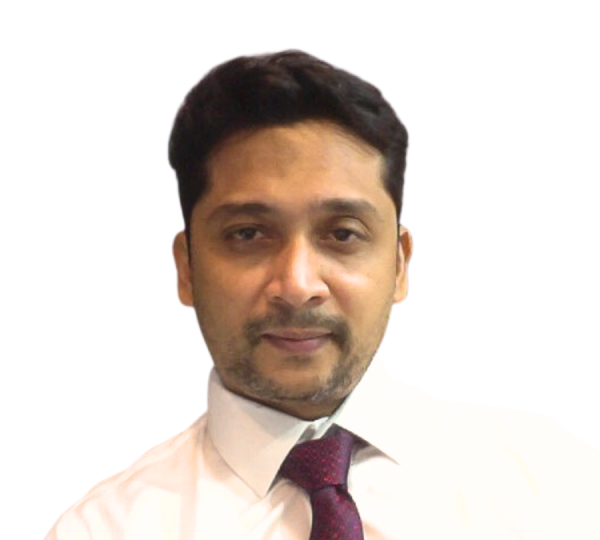
What are the most significant technological breakthroughs in jewellery manufacturing that have occurred in the last five years? This is across areas like CAD/CAM, Advanced Materials, New Alloys, Gemstone Cutting and Setting, 3D Printing, Automation, Blockchain, AI plus any other.
India’s jewellery manufacturing business has seen rapid growth over the past decade, and this has led to several innovations and changes in the jewellery manufacturing processes. One of the key drivers of technological change is the demand for new designs by end customers that has forced greater adoption of CAD/CAM technologies.
Traditional mold-based processes that were used to produce hundreds of similar designs had to be replaced by direct manufacturing processes where each design is printed and then casted directly in limited quantity. This led to the adoption of 3D printers in wax and direct castable resin that have the ability to adapt to ever changing designs.
Organic shapes, which can be created by new software tools like Zbrush, are inspiring new designs that challenge traditional manufacturing methods. To produce these complex shapes, processes such as electropolishing are becoming more popular, as they can handle the complex profiles that manual finishing methods cannot.
On the other hand, gold prices are driving demand for very lightweight jewellery that can be only produced by CAD/CAM and advanced casting machines that are able to cast very thin profiles. These profiles are then very difficult to finish using manual methods hence paving greater adoption of automation in finishing techniques.
We are also seeing greater automation in jewellery processes that had almost zero automation such as stone setting. Robotic systems are now available that are able to set stones on a mass scale on jewellery of certain design styles.
Cutting-edge CNC systems are pushing the limits of technology in several jewellery categories such as CNC cut bangles, die-made stamped jewellery and many more such segments. We are also seeing emergence of additive manufacturing systems that are having the ability to directly print gold by using SLS-based (Selective Laser Sintering) 3D printing.
Newer alloys are now offering more options for the buyer in terms of colours and carats and the market for 10k, 14k gold jewellery has just begun. On the marketing front, jewellers are now seen to be more confident in investing in e-commerce channels to boost sales. A whole segment of new technologies have emerged in boosting the ability of the jeweller to go online that include automated photography, augmented reality (AR), VFX, virtual showrooms, RFID, marketplace e-commerce, etc.
Overall, the technological enhancements seen in jewellery manufacturing in the past 5 years is unprecedented, paving way for better designs, finish and productivity.
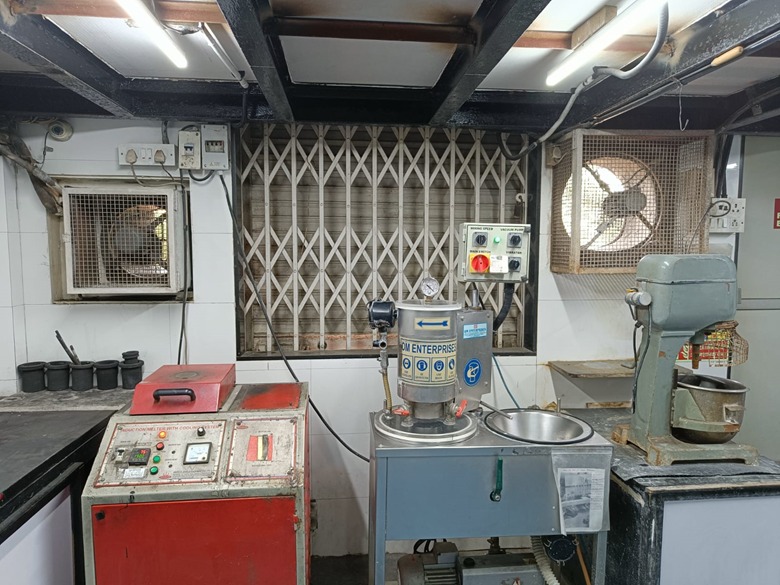
What trends/developments do you anticipate in jewellery manufacturing technology over the next 5 years, and how might these impact the industry?
The next 5 years would see a greater adoption of CAD/CAM systems, automation systems in various aspects of jewellery manufacturing such as casting, stone setting, etc. and automated finishing systems such as electropolishing. There could also be some adoption of direct manufacturing systems using additive manufacturing with the ability to directly produce gold patterns. The demand of lightweight gold jewellery would increase if the gold prices continue to soar and that would mean manufacturing processes for making lightweight jewellery.
Making lightweight jewellery using electroforming methods would continue to grow and so will the use of CAD/CAM and manufacturing methods for wire mesh jewellery. The trend for 10k, 14k and fashion jewellery would bring newer alloys and metal combinations to the forefront and manufacturing processes for producing unique metals such as titanium, steel, etc. would have a greater role.
What new technology / processes can manufacturers integrate to cut gold wastage & costs, speed up studded jewellery production, and improve quality?
To begin with CAD/CAM is extremely important for every jeweller that does casted jewellery. This would significantly reduce time, reduce cost and improve quality. Professional casting systems and materials also improve quality, thereby reducing the need for heavy polishing methods and if combined with a good electro-polishing system, it can significantly reduce wastage, labour and costs. Automation in stone setting is in its infancy now, however, once adopted fully, this could lead to enormous cost cutting and time saving.
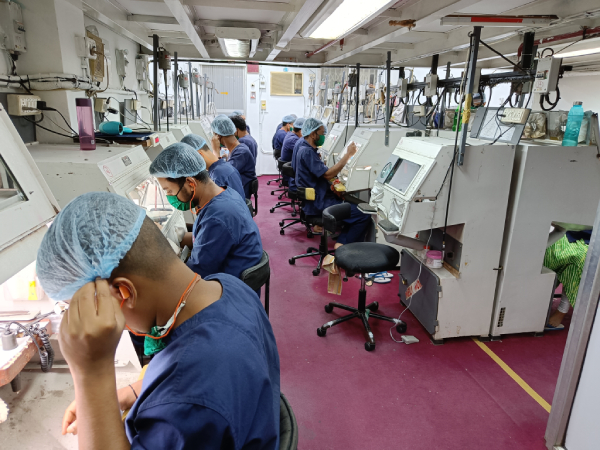
Are we in danger of losing traditional jewellery craftsmanship skills to modern technology, or will the two coexist?
Traditional jewellery craftsmanship has its own place especially in India. Although more and more automation is seen in casted and machine-made jewellery, the traditional craftsmanship still exists in handmade gold jewellery and this market is still very active in India. This type of craftsmanship is also seen in kundan jewellery and constitutes a very big market especially the bridal segment.
Traditional craftsmanship is not likely to decline, as there is still a demand for handmade jewellery in India. However, finding skilled workers for these segments is a challenge. These categories have not seen much technological advancement, as they depend on manual labour. Therefore, traditional hand-made jewellery and jewellery craftsmanship will coexist with modern technology for the foreseeable future.
Is the Indian jewellery industry developing its own indigenous technology that incorporates traditional elements and techniques?
There is no doubt that indigenous technology has always been present in the Indian jewellery industry with many machines developed and made in India since many decades. These include machines in the area of chain making, casting, ball cutting, die making and stamping, etc. India has always been a hub for jewellery machines and even an exporter in several segments.
However, in recent times, innovation is also happening in certain high-technology areas such as 3D printing, electropolishing, CNC machines, etc. where earlier only European companies were present. This is extremely encouraging and in sync with India’s technological growth.
Several companies providing IT solutions around jewellery manufacturing are also playing a key role in the global jewellery market. India has always been a key player in the global jewellery market and with these technological developments we are all set to continue to dominate this market.