Whistle while you work is the maxim close to this celebrated artisan’s heart. If he doesn’t enjoy what he does, he discards the project – as simple as that. It’s more about ‘play at work’ – an aspect deeply forged into his work philosophy.
Meet master metalsmith and twice winner of Santa Fe Symposium’s Industry Leader Award, CHRIS PLOOF, Designer and Founder of Chris Ploof Designs, Massachusetts, who enjoys teasing out beautiful forms out of bio-compatible Damsascus steel, meteorite, palladium, platinum, gold, and is known for his application of Mokume Gane, an ancient Japanese metalworking technique that produces wood-grain patterns, in his jewellery.
Chris Ploof is a genius, a master metalsmith, who considers himself fortunate to enjoy what he does best – melting, moulding, and manipulating metals to forge new shapes in the form jewellery. Each piece is as unique as the person who wears it. “We use our heads, we listen to our hearts, and we make with our hands,” he says.
Tell us about your early years … you were always enraptured by metalwork, and the use of different material/ metals … You have always been a hands-on artist. Before designing jewellery, what was your profession?
I’ve always been very creative, and engineering minded. I do love using my hands and my head!
My early years as a very young child were filled with play with various building toys and, much to my mother’s dismay, disassembling mechanical items around the house.
When I was old enough to start working and have a career, I worked as a mechanic in the bicycling industry. I worked as a sales manager and service manager to a team mechanic for both men’s and women’s cycling teams.
Eventually, I become the head mechanic and trainer of a multi-store bicycle retail chain.
What was the turning point that made you shift to contemporary jewellery designing?
I wanted to learn how to cast some metal pieces to make a few tools out of aluminum for bicycle repairs, so I enrolled in a night class for jewellery casting. I thought the knowledge would allow me to accomplish my toolmaking goals.
However, in the process, I discovered the smaller scale world of jewellery, and loved it! I was instantly hooked.
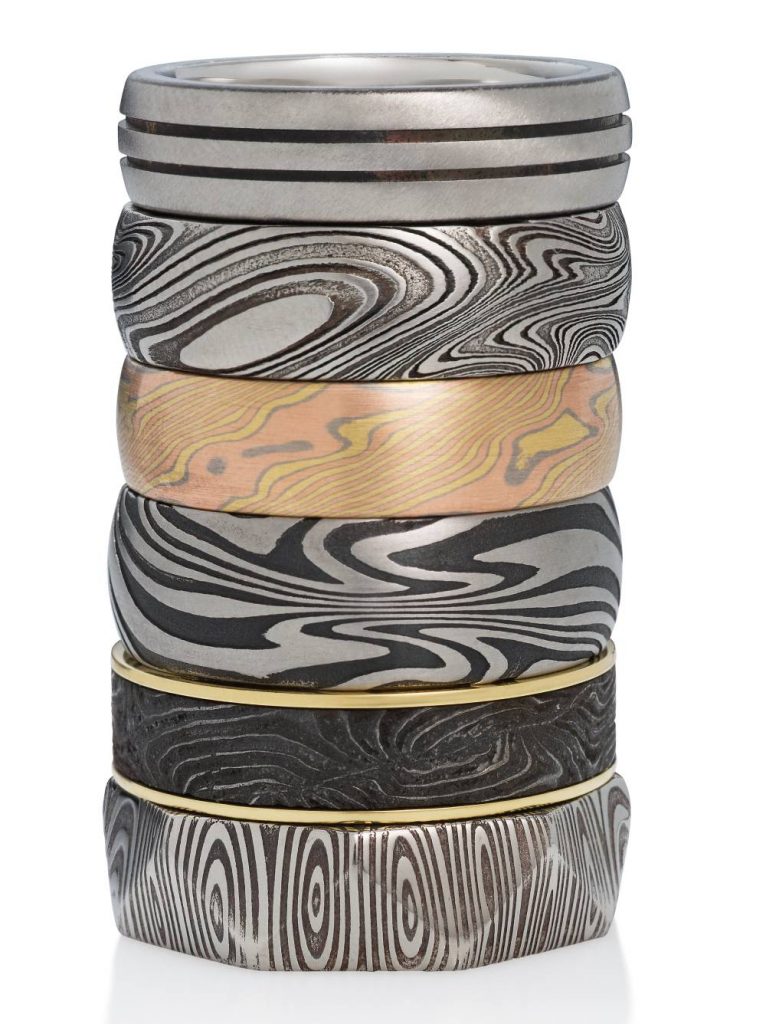
When did you establish Chris Ploof Designs?
I started making my first pieces of jewellery in the late 1990s. By 2004, I had officially started my company and began selling in the United States and in other countries.
Many jewellery artists start off with an inspiration to begin with … and leave it to the technicians and artisans to execute the final piece. You definitely love to experiment with different metals. Tell us how is a piece of jewellery realised from start to finish in your atelier?
Generally, my designs start with an idea, a vision of the finished piece. Many times, it is really an incomplete vision – meaning as we make the piece, the design may evolve or change. Some of this is dictated by aesthetics, but typically, we make changes based on the materials we are using.
We are masters of use of some very difficult techniques and metals (for example, Mokume Gane, Damascus Steel, and Meteorite). By necessity, this influences how we make our pieces. We also are known to discuss pieces as a group as they are taking form – we like to have fun at work and have actually stopped making some designs because we didn’t enjoy them.
Which are the methods/metals that you love to work with and why? What impels you to take the paths unknown?
We use the process of Mokume Gane in our work, a precious metal lamination technique that allows us to create wood grain patterns.
Damascus Steel is a favourite material – we laminate, forge, and twist 304/316 steel into bars and sheets to produce rings (especially wedding bands) and other types of jewellery (pendants, cuff bracelets, bangles, earrings, etc.) We are so adept at creating beautiful patterns for a fair price. We sell large quantities of this material to other jewelry manufacturers in the United States, China, Finland, Sweden, Thailand, and Canada. We also sell this material to people outside of the jewellery industry (like knife makers) who desire to make items out of our patterned Damascus steel. Over the past few years, we have been working with the high-end audio industry making materials used to produce in ear monitors (IEMs).
People can see some of the processes we use in this new video below.
Your art is backed by years of research that goes on in the backend before you wow the world with your work. I’m sure you must have faced many disappointments at the work bench. Does it frustrate you or do you have a fun approach to work?
For me, if it’s not fun, I don’t do it. And that fun can lead to frustration. But the joy of solving a difficult problem makes it all worthwhile in the end. Never give up!
You have a superb hold over technical aspects of jewellery making… how do you balance the act between being a designer and a metalsmith?
I don’t consider myself a designer in the traditional sense – the patterns in the materials dictate a lot of form and function for me. I think, in order to be a maker of jewellery, the more science (metallurgy and metalsmithing) you bring, the better your designs become. You have to really understand your materials and their individual properties in order to make high quality items. Without this understanding, you can’t push the envelope of possibilities and designs.
How long does it take for each collection to come to life?
We have had some collections come to life in a few days, and some take months. It really depends on what we are trying to do. But also, it can depend very much on how excited we are to do it!
The achievements you are proud of in terms of metals used and designs?
I’m a big fan of our Damascus steel products. Making Damascus is easy with carbon steel materials, and this creates good, very strong knife steel. But it can be terrible for jewellery because it rusts and corrodes easily.
However, our 304/316 Damascus steel is very difficult to make and uses a proprietary bonding method we have developed. This means it endures and stands the test of time. The Damascus steel jewellery and rings we make are good enough to endure as bridal rings and wedding bands! I am proud of that.
We would like to know your design philosophy.
Clean lines that help showcase the pattern of the material, make it look simple even if it is difficult to make. Everything has to be wearable and comfortable, and it needs to be of heirloom quality.
If you were not a jewellery designer, what would you be?
I’d still be a bicycle mechanic. Or maybe an electrician…
What is a day in the life of Chris Ploof?
I keep a very busy schedule. I’m awake early and spend time looking at new work, designs, inspirations, materials and doing some technical research.
Then I head to the workshop, where I immediately “dive in” to small tasks and responding to emails.
Soon after that, I’m at work crafting and creating – it may be sketching, but typically, it’s more hands on work – forging, machining, fabricating…
Then, I have lunch, and return to more of the same until I head home. My wife and I usually cook dinner together, and then I do more design and research work, followed by some pleasure reading before bed.
What are your hobbies?
Mountain biking, road cycling, cooking, gardening, reading, and board games.
Do you follow any Indian designers?
I don’t follow any specific Indian designers, but I do follow a few stone cutters. I’ve been asked to come to India a few times for consulting and teaching Mokume Gane, but that was just before Covid stopped all travel. I would like to visit India. We will have to see what happens!
Read more about Chris Ploof at https://chrisploof.com