Our Singapore-based special correspondent RICHA GOYAL SIKRI reveals how Gemfields’ transparent and well-run operation has transformed the local ecosystem and community around the Kagem emerald mine in Zambia.
“213 grades of rough emeralds at auction?! What’s the secret?” I asked, still processing the statistic. “Why don’t you visit Kagem, our emerald mine in Zambia, and find out?” replied Dr. Sixtus C. Mulenga, chairman, Kagem Mining Ltd. I laughed out loud, thinking he was joking. That was in Singapore in November 2018.
The late 1970s saw the discovery of emerald deposits in Zambia, and Indian manufacturers have been sourcing since then. The first official auction for Zambian emeralds was held in June 1982 by the Reserve Mineral Corporation, a government entity. Dharmendra Tank from Tank Fine Gems, who attended that auction, remembers it well, “On arrival, we were ushered into a big office and presented with four grades of emerald lots to view. While there were approximately 8-10 companies invited, only three travelled to Lusaka for the auction. As those were the formative years, there was no competition at that auction. There would be 10-15 lots, and around that many bidders, so everyone was quite comfortable in the knowledge that they would go home with something.”
The story of Zambian emeralds took an exciting turn in 2001 when the government privatised the Kagem mine and established a 55:45 joint venture with HAGURA (owned by Harel, SS Gupta & Rao). HAGURA subsequently increased their shareholding from 55% to 75% in 2005, with the government holding the balance 25%. During this period, the Kagem mine was producing emeralds through openpit mining, unlike the underground operations in Colombia.
While the company was also selling emeralds and beryl through auctions, probably due to the nascent stage of the sector, some crucial factors were missing. First, the focus was on short-term mining, rather than investing in scientific geological data. Due to this, the shape of the open-pit was haphazard, making working conditions unsafe and damaging for the environment. Second, since the discovery of the deposit, people from different geographies of Zambia were migrating with their families to the area surrounding Kagem, in the hope of ‘striking it rich’. Some of them, after exhausting their limited funds, and unable to return to their villages, found themselves destitute, and in desperation, resorted to criminal activities. These circumstances, combined with a de-motivated workforce at Kagem, and a lack of community engagement, resulted in high pilferage and strong resentment against the mine in the district.
The story of the Kagem emerald mine switched into high gear in October 2007 when Pallinghurst bought 100% of HAGURA. In July 2008, it sold HAGURA to Gemfields Resources plc in return for its shares, thereby acquiring control of Gemfields, which became the 75% shareholder of Kagem Mining Ltd. and a partner with the Zambian government, who were still holding the balance 25%.
Emerald mining is particularly complex due to two factors – first, the crystal-bearing rocks are found deep in the Earth’s crust, which means a sizeable chunk of land needs to be unearthed to reach them. Second, emeralds form only when the 1.7 billion-year-old TMS rock (talc magnetite schist) bearing chromium and vanadium (the colouring agents), interacts with a 500 million-year-old pegmatite rock, which contains beryllium. Where these two rocks intersect, if you are lucky, you may find a ‘reaction zone’ containing emeralds and beryl.
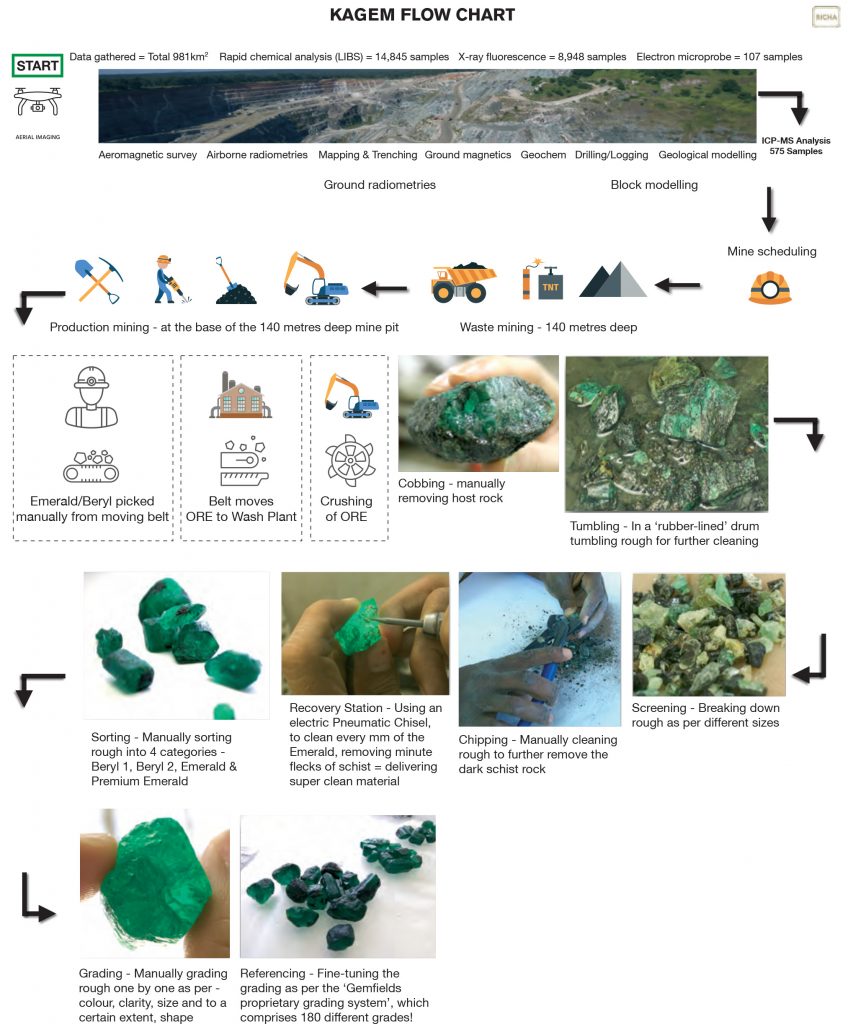
The Kagem mine today is considered the largest emerald mine in the world, with its central ‘Chama pit’ 2km long and 140m deep, and responsible for 25-30% of global supply.
There are two elements involved in the mining process – first is “waste mining”, which involves unearthing a significant crosssection of land to reach the ‘reaction zones’. While waste mining involves usage of blasting techniques, there is no impact on the emerald deposit due to the distance from the ‘reaction zone’. The second element is “production mining”, where geologists are primarily considering areas where the TMS rock is interacting with the pegmatite rock, hoping to find ‘reaction zones’. Once a reaction zone is discovered, an eight-person crew – a geologist, four to five chisel-men, and two security personnel – manually extract and secure the crystal-bearing rock in a numbered red metal container. Liberated crystals are sent directly to the sort house, whereas emeralds trapped inside the host rock are further processed in the wash plant.
There are 1,000 people working and living at the Kagem emerald mine. Workers with families in Kitwe return for the weekend, and the rest permanently stay on-site. It is estimated that each worker has typically five to seven dependents, making the economic ripple effect of this large-scale operation significant.
Jack (name changed), one of the drivers at Kagem, tells me, “I used to work odd jobs in Kitwe on an ad-hoc basis; sometimes as a mechanic, for a couple of months installing satellite dishes. There was a lot of instability in my life. When Gemfields took over the Kagem mine and started expanding the operation, it created a lot of jobs. I applied at the mine and I am happy working at Kagem now for seven years. I have a stable income, which allowed me to get married, start a family and build a good life for myself.”
In large-scale mining, long-term sustainability of the operation and community relations are both important for exponential growth. In 2008, the new Kagem team were at a crossroads: should they take the current stock-in-reserve to market, or focus on cleaning house first? They decided to wait and began investing time and resources in correctional works, adopting a scientific approach, which meant moving two years of old waste, re-shaping the open mine pit for safer working conditions. They also accelerated production to build their emerald and beryl inventory.
Around a decade ago, gem manufacturers in India were sourcing emeralds of diverse origins from various suppliers, but the primary challenge they faced was inconsistently graded material, and on many occasions, emerald crystals still embedded in the host rock.
While the Kagem mine, before 2008, regularly conducted auctions offering graded emeralds, the best lot at the time of auction would automatically be classified as ‘Grade A’. Inconsistency in the lots available meant the definition of ‘Grade A’ varied from one auction to the next. Further, despite established ‘reserve pricing’ for a lot, an ad-hoc sale would still be undertaken below reserve.
For a gem manufacturer, time is money. He or she needs to produce and sell at a steady pace to keep the wheels turning. The probability of a sale increases significantly when the product offered is homogenous. “At that time, if I wanted to create a layout worth $200 per carat, I would have no choice but to buy a ‘mixed lot’ of rough emeralds, containing both lower and higher priced goods. While my target range would quickly sell, I would get stuck with slow moving, lower rated products, wasting precious time and resources,” notes Sumit Mehta, a Zambian emerald specialist, based in Jaipur.
What lies beneath
When I first held a rough emerald, I thought this was the original form in which they were plucked out of the ground. I didn’t realise that to extract a small emerald, years of geological surveys are conducted over vast mining concessions. At Kagem, the team has employed aeromagnetic surveys and airborne radiometries to collate scientific data for approximately 981 sq km. This vast repository has been further sliced via ground magnetic research, geochemical analysis, mapping, trenching, drilling, 3D modelling of the land, to name a few. I was informed, as per industry-wide exploration standards, Gemfields today has the most comprehensive range of data density in the coloured gemstone mining sector, and absorbing the three-hour long geology session, I could believe it.
To put the rarity factor of emerald discovery in perspective, in metal (copper) mining, 4 tonnes of waste = 1 tonne of ore, out of which you are relatively confident of 1% of copper (or 10,000 grams). In contrast, in emerald mining, 87 tonnes of waste = 1 tonne of ore, which in turn may generate on an average only 50 grams of emerald (or 0.005%). At Kagem, they move 1 million tonnes of rock every month, and 70% of the revenue comes from only the top 7% of production!
While the star performers in this story may be the top grade emeralds, to find them, the entire production of the mine has to go through multiple processes as shown in the flow chart. While studying these steps, I was most impressed with the ‘recovery station’, where a very experienced gentleman was patiently removing dark grey schist rock from each emerald, with a hand-held pneumatic chisel, like a dentist cleans teeth!
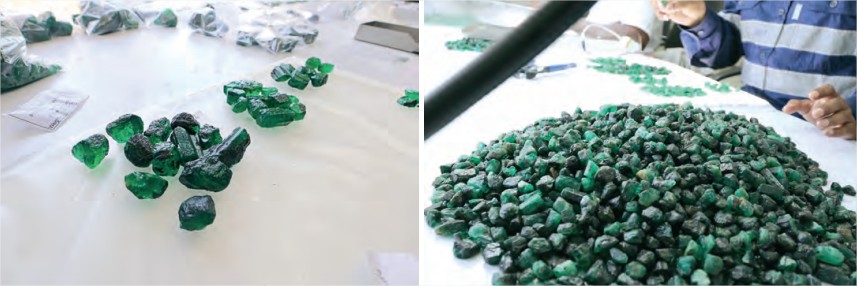
“We spend considerable time and resources to remove as much of the host rock as possible. This provides our customers with clean crystals, enabling them to effectively evaluate the material for bidding and reduce their manufacturing timeline,” says Jackson Mtonga, assistant sort house manager.
The Kagem mine 2.0 conducted its first formal auction in July 2009, where they presented the industry with their proprietary and fairly exhaustive formula for grading rough emeralds across 180 categories, segmented as per facet, colour, size, clarity and to a certain extent, shape. The sort house team undertakes this important task of sorting, grading and fine-tuning the categorisation of the material using the Gemfields reference set, which is their ‘Coca-Cola’ equivalent formula. Today, the company offers emeralds graded across 213 categories.
While numerous mining licences surround the Kagem mine, it’s difficult to estimate how many are effectively producing due to the heavy investment required in equipment and expertise. The presence of illegal miners further complicates matters.
Paragraph 35.1 of the Mines and Minerals Development Act (2015, as amended) states that “The holder of a mining licence shall… (L) maintain security and ensure that there are no illegal miners at the licensee’s tenements.” However, a short drive away from the Kagem mining concession brought us to a dump site, which was crawling with illegal miners. We witnessed one of the trucks of another mining company emptying their load onto a large group of illegal miners, who were precariously balancing themselves on the edge of a high waste mountain. Some may argue, since the mining company is permitting the miners on their dump, they should not be considered “illegal”, however, the law is quite clear as stated above. This dark side of the business does sometimes cast its shadow on the work at Kagem, as the mining staff are frequently targeted by syndicates who then pressurise or threaten them to assist with theft. To protect the identity of the workers, we were under strict instructions to not take or post any photographs showing the faces of the crew. On the subject of facilities, Ms. Gertrude, spokesperson for the Zambian Association of Women in Mining, explains, “Availability of clean water, medical facilities and police posts are integral to the future development of women in mining in Zambia. Due to this, we are currently seeing very limited activity among members. The availability of the Nkana clinic and hospital, established by Kagem Mining Ltd., is an important enabler for small-scale operations in the region. If we had more companies contributing like Gemfields, things would be easier.”
Given that ten years ago, the emerald mining sector delivered practically zero revenue to the government, it’s encouraging to learn that in 2014 Kagem set a record for the highest contribution of $35 million to the Zambian government. In 2016, it again came close with a contribution of $34.1 million.
Further, one-quarter of Kagem’s total revenue is spent on taxes, royalties, conservation support to the Zambian Carnivore project and community programmes, such as the Kapila primary and Chapula secondary schools with 300 and 1,000 students respectively; the Nkana clinic and hospital, which treated 20,000 patients in 2018; and four farming cooperatives that they helped establish and support.
“None of this would be possible without the support of the Indian gem manufacturing sector, which represents 95% of our emerald customers. While the recent slew of challenges in India have impacted the overall market, and resulted in softer bidding, due to demonetisation, increased regulation, taxation, and pressure on liquidity, it’s encouraging to note the current price stability for premium grade emeralds, being $68.03 per carat in November 2018 (only 3.8% below the $70.68 per carat peak of April 2016),” says Adrian Banks, director of product, Gemfields.
As I am guided around the Chapula secondary school, by a confident 16-year-old student, Ms. Musukwa, I ask her about her plans after school. She looks me straight in the eye and says, “I want to become a nurse and help our community.” Less than a decade ago, she would have had no option but to stay at home and comprehend a future without the advantage of education.
Packing my bags, I find myself thinking about the impression of large-scale mining I had from afar, what different people had told me, and the questions I had in my mind. While I may not have all the answers to the complexities surrounding the debate of large-scale mining, one thing I know for sure—there is a place in the Copperbelt region of Zambia, where they believe themselves to be ‘custodians’ of an emerald deposit that, in true nature, they say belongs to the land, where they respect the ecosystem through responsible extraction, where they optimise value by bringing that deposit to market in a professional and transparent manner, and where they deliver the maximum benefit for the workers, children and the community at large, and that place is a land called Kagem.